Packaging Machine Repair Service: Guaranteeing Marginal Downtime and Maximum Performance
Packaging Machine Repair Service: Guaranteeing Marginal Downtime and Maximum Performance
Blog Article
Understanding the Secret Components and Repair Work Strategies for Packaging Machine Upkeep
Reliable upkeep of product packaging machines depends upon a thorough understanding of their crucial parts, including the frame, drive system, and sealing systems. Recognizing common maintenance concerns, coupled with the application of preventative strategies and repairing techniques, can significantly boost maker reliability. The option of fixing practices, including the usage of OEM components and the importance of licensed service technicians, plays a vital duty in minimizing downtime. To really understand the details of these systems and their maintenance, one must take into consideration the more comprehensive ramifications of neglecting these important methods.
Trick Components of Packaging Makers
Product packaging machines consist of numerous essential components that function with each other to ensure reliable and reliable packaging processes. At the core of these makers is the frame, which offers architectural honesty and houses the numerous operating components. The drive system, frequently a mix of motors and gears, assists in the movement of components, enabling accurate operation throughout the packaging cycle.
An additional crucial component is the conveyor system, which delivers products through different stages of the product packaging procedure. This is commonly matched by sensors and controls that monitor the position and rate of things, guaranteeing synchronization and reducing errors. The filling system is critical for properly giving the ideal quantity of product into packages, whether in fluid, powder, or solid form.
Securing systems, including warmth sealers or sticky applicators, play a vital role in safeguarding packages, stopping contamination and prolonging service life. In addition, labeling systems are important for offering needed product details, guaranteeing compliance with guidelines. The control panel, geared up with easy to use user interfaces, enables operators to take care of device features, monitor performance, and make changes as needed, guaranteeing optimum productivity and effectiveness in packaging procedures.
Usual Maintenance Concerns
Efficient operation of packaging machines depends greatly on normal upkeep to avoid typical issues that can disrupt production. Amongst these concerns, mechanical deterioration is widespread, especially in parts like conveyors, motors, and seals, which can bring about unanticipated downtimes. Furthermore, imbalance of parts can cause inefficient procedure, triggering items to be improperly packaged or harmed throughout the process.
An additional usual upkeep problem includes the accumulation of dirt and particles, which can interfere with the device's sensors and moving components. packaging machine repair service. This not just affects efficiency yet can also pose safety and security risks. Lubrication failures can lead to enhanced friction, resulting in getting too hot and eventual part failure.
Electrical troubles, frequently coming from loosened links or worn-out electrical wiring, can disrupt equipment functions, causing substantial manufacturing hold-ups. Finally, software program glitches as a result of outdated programs or inappropriate setups can impede the device's procedure, demanding prompt intervention. Addressing these typical upkeep concerns proactively is crucial for ensuring optimal performance and long life of product packaging equipment.
Preventative Maintenance Strategies
Carrying out preventative maintenance approaches is crucial for sustaining the efficiency and integrity of packaging equipments. These methods include a systematic strategy to upkeep, focusing on the regular assessment and maintenance of equipment to preempt potential failures. By adhering to a scheduled maintenance program, drivers can identify wear and tear on parts before they cause substantial breakdowns.
Crucial element of a preventative maintenance method include regular examinations, cleansing, lubrication, and part replacements based upon producer recommendations. Using checklists can streamline this procedure, making sure that no essential her response tasks are overlooked. Additionally, keeping precise documents of maintenance activities help in tracking the equipment's efficiency gradually, promoting notified decision-making relating to future upkeep needs.
Training personnel on the relevance of preventative upkeep improves compliance and cultivates a society of aggressive care. Applying a predictive maintenance component, using data analytics and sensing unit technology, can better maximize machinery performance by anticipating failures before they occur.
Troubleshooting Methods
When confronted with malfunctions or inefficiencies in product packaging devices, employing methodical troubleshooting techniques is crucial for determining and resolving problems swiftly. The primary step in effective troubleshooting is to develop a clear understanding of the machine's operational specifications and efficiency metrics. This includes assessing the machine's requirements, as well as any kind of error notifies or codes shown.
Next, drivers ought to carry out a visual examination, checking for noticeable signs of damage, wear, or imbalance. This frequently consists of analyzing gears, sensors, and belts to pinpoint potential reasons for malfunction. Gathering functional data, such as manufacturing rates and downtime logs, can likewise offer insights right into persisting issues.
Once potential troubles are determined, utilizing a rational technique to isolate the root cause is important. This may require testing specific parts or systems in a controlled way. Taking part in discussions with operators who communicate with the machinery on a regular basis can produce important comments about uncommon habits or patterns.
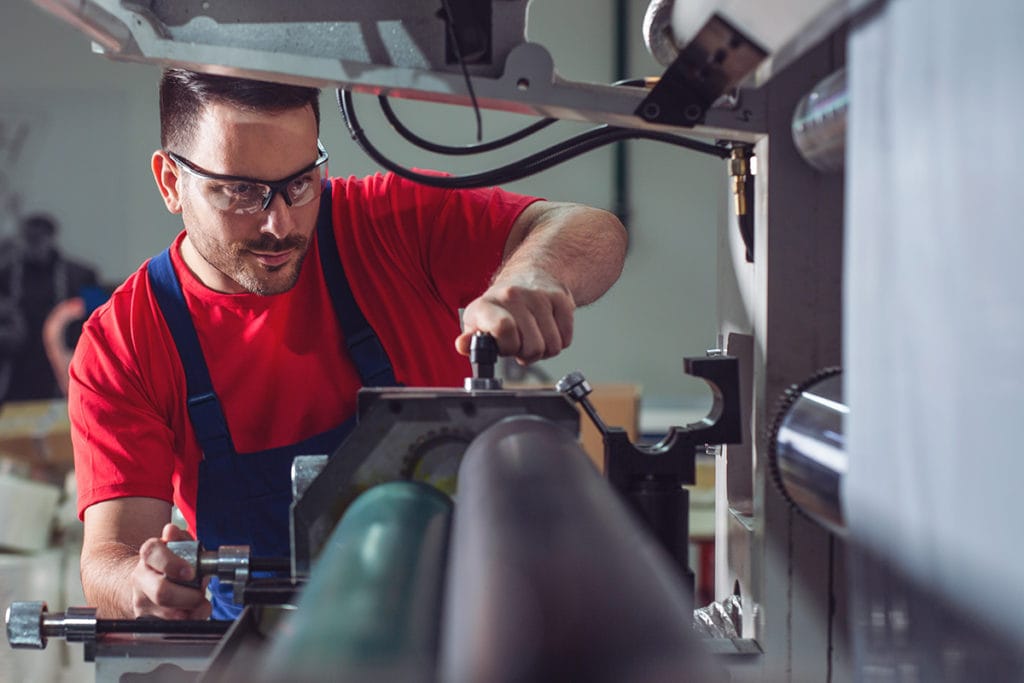
Repair Work and Substitute Ideal Practices
A comprehensive understanding of repair work and substitute ideal methods is important for keeping the long life and efficiency of product packaging equipments. Consistently examining the problem of device elements permits timely treatment, protecting against more considerable concerns that can lead to expensive downtimes.
When repairs are essential, it is necessary to use OEM (Original Equipment Supplier) components to make certain compatibility and performance. This not just preserves the honesty of the device however likewise supports service warranty arrangements. In addition, it is a good idea to maintain a supply of crucial spare parts to facilitate quick replacements and decrease functional disturbances.
For intricate fixings, engaging qualified specialists with specialized training in product packaging equipment is advised. They have the know-how to detect issues accurately and execute fixings effectively. Recording all fixing tasks and components substitutes is critical for maintaining an extensive maintenance background, which can aid in future troubleshooting.
Last but not least, executing a positive approach, consisting of regular examinations and predictive upkeep strategies, improves the integrity of packaging machines. By adhering to these best techniques, companies can make sure ideal machine efficiency, reduce functional risks, and extend tools life site web expectancy.
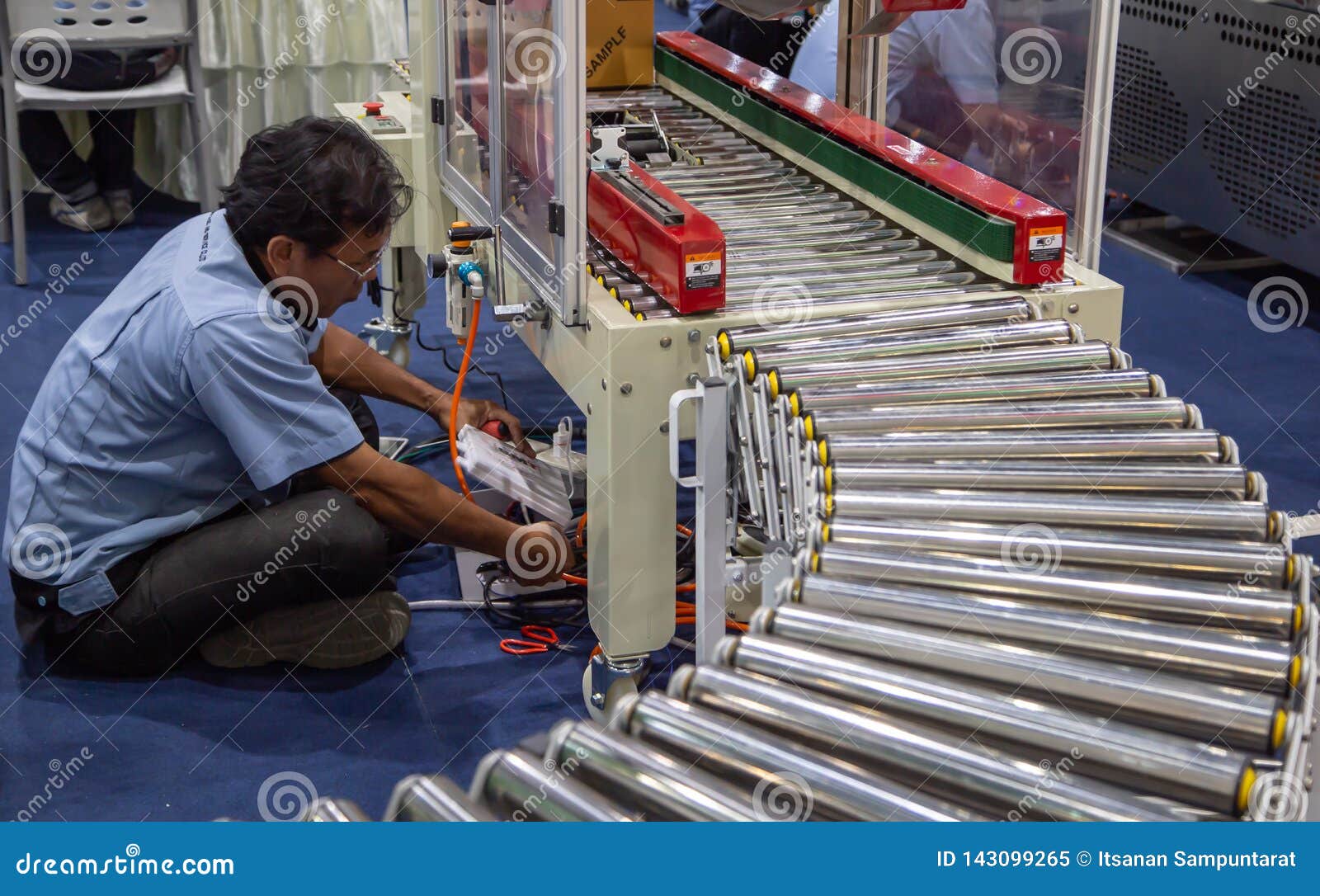
Conclusion
In final thought, an extensive understanding of packaging maker elements and effective maintenance methods is essential for optimal performance. By carrying out these techniques, organizations can ensure the longevity and effectiveness of packaging devices, eventually contributing to improved functional performance and reduced costs (packaging machine repair service).
Reliable maintenance of product packaging machines hinges on a comprehensive understanding of their key parts, including the structure, drive system, and securing mechanisms.Effective procedure of packaging equipments relies greatly on routine upkeep to prevent usual concerns that can interrupt manufacturing.Implementing preventative maintenance approaches is important for sustaining the efficiency and reliability of go now product packaging machines. In addition, keeping precise records of maintenance tasks aids in tracking the machine's efficiency over time, helping with informed decision-making pertaining to future upkeep requirements.
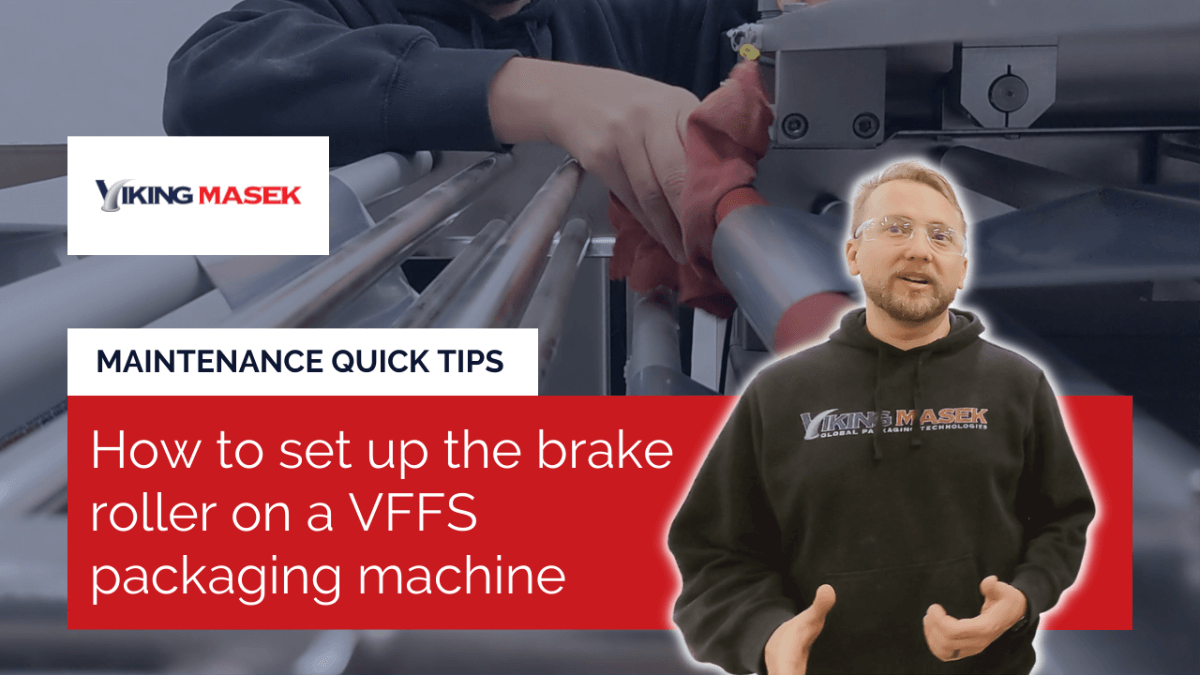
Report this page